產(chǎn)品展示
| PRODUCT您的當(dāng)前位置:首頁 > 新聞動(dòng)態(tài) > 產(chǎn)品知識(shí) > 正文
正文
高爐、焦?fàn)t、鉛熔煉爐用耐火材料介紹
發(fā)布時(shí)間:2021/7/29 17:36:22 點(diǎn)擊率: 來源:高鋁磚廠家 作者:榮盛耐材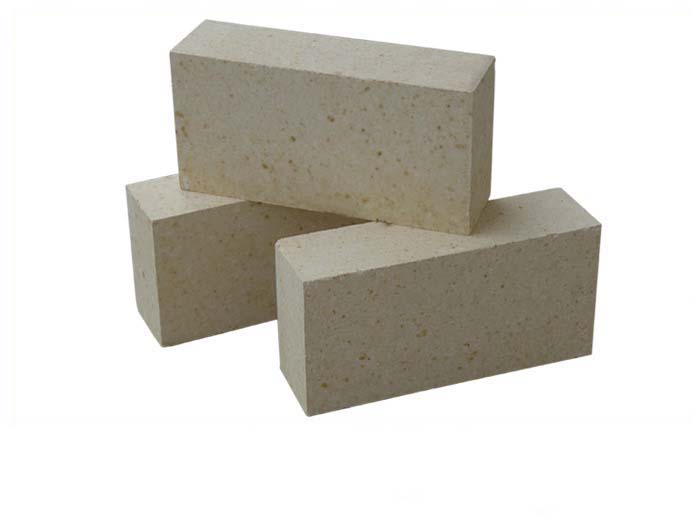
用于高爐冶煉的原料主要是鐵礦石、燃料(焦炭)和熔劑(石灰石)三部分。一般情況下,冶煉1噸生鐵需要1.5-2.0噸鐵礦石、0.4-0.6噸焦炭、0.2-0.4噸熔劑,總共需要2-3噸原料。要保證高爐連續(xù)生產(chǎn),就需要充足的原料供應(yīng)。所以,無論是生鐵廠家還是鋼廠原材料采購(gòu)工作尤為重要。
因?yàn)楦郀t是連續(xù)生產(chǎn)的,所以一代高爐(從開爐到大修停爐為一代)可以連續(xù)生產(chǎn)數(shù)年至十幾年。在生產(chǎn)過程中,從爐頂(一般爐頂是由料種與料斗組成的,現(xiàn)代化高爐是無料鐘的爐頂和爐頂)不斷地將鐵礦石、焦炭、熔劑從高爐下部的風(fēng)口吹入熱風(fēng)(1000~1300℃),并噴入油、煤或天然氣等燃料。裝在鼓風(fēng)爐里的鐵礦石,主要是鐵和氧的化合物。該過程稱為還原,在高溫下,焦炭中和噴吹物中的碳與燃燒產(chǎn)生的一氧化碳將鐵礦石中的氧奪走,得到鐵。鐵礦經(jīng)還原反應(yīng)煉鐵,從出鐵口放出鐵水。礦脈石、焦炭、噴吹物中的灰分與加入爐內(nèi)的石灰石等熔劑結(jié)合,形成從出鐵口和出渣口各排出渣。氣體由爐頂排出,除塵后作為工業(yè)氣體使用。現(xiàn)代高爐也可以利用爐頂高壓,部分外排氣體發(fā)電。
爐體由上至下分為爐喉、爐身、爐腰、爐腹、爐缸5部分。因高爐煉鐵具有技術(shù)經(jīng)濟(jì)指標(biāo)好、工藝簡(jiǎn)單、生產(chǎn)能力大、勞動(dòng)生產(chǎn)率高、能耗低等優(yōu)點(diǎn),故該方法生產(chǎn)的鐵占世界鐵總產(chǎn)量的絕大部分。在高爐生產(chǎn)過程中,將鐵礦石、焦炭、造渣用熔劑(石灰)從爐子下部沿爐周的風(fēng)口吹入預(yù)熱的空氣。一氧化碳和氫氣在高溫下燃燒焦炭產(chǎn)生的一氧化碳和氫氣,在爐內(nèi)上升時(shí)將鐵礦石中的氧去除,從而還原成鐵。煉鋼的鐵水從鐵口排出。鐵礦中未還原雜質(zhì)與石灰石等熔劑結(jié)合形成爐渣,從渣口排出。排煙氣由爐頂排出,經(jīng)除塵后用作熱風(fēng)爐、加熱爐、焦?fàn)t等燃料。爐渣生產(chǎn)的主要產(chǎn)品是生鐵,還是高爐渣和高爐煤氣的副產(chǎn)物。
a,用于爐體上部的耐火材料:
主要原因:機(jī)械侵蝕、空氣流動(dòng)、爐料磨損及溫度劇烈變化引起的熱負(fù)荷劇烈變化,工作環(huán)境非常惡劣。
所以,該部位推薦使用耐化學(xué)腐蝕、耐磨損、耐剝落、導(dǎo)熱性能好的氮化硅碳化硅磚。
爐身中部用耐火材料:為有效防止?fàn)t內(nèi)高溫氣流的劇烈沖刷,保證爐襯的導(dǎo)熱性,降低爐襯溫度和侵蝕,推薦使用高質(zhì)量的氮化硅碳化硅磚或賽隆硅磚。
爐身下部:爐身下部為鑲磚冷卻壁結(jié)構(gòu),爐體下部為初渣區(qū),為有效阻止初成渣和高溫爐氣對(duì)爐襯的雙重劇烈侵蝕,爐襯采用抗熱沖擊性好、高溫強(qiáng)度高、導(dǎo)熱性好的耐火材料,根據(jù)近幾年國(guó)內(nèi)外的高爐內(nèi)襯設(shè)計(jì)經(jīng)驗(yàn),在爐身下部選用抗熱沖擊性好、高溫強(qiáng)度高、耐高溫性能好的耐火材料。
d、爐腰、爐腹耐材:爐腰/爐腹承受較高的溫度,耐火材料的損壞程度接近或超過爐身下部。為了防止渣皮、堿金屬的侵蝕和高溫氣流的沖刷,故該部位仍采用抗熱沖擊、高溫強(qiáng)度高、導(dǎo)熱性好的Sialon-SiC磚或Sialon-Al2O3磚或Sialon-Al2O3磚。
風(fēng)口區(qū):風(fēng)口區(qū)溫度波動(dòng)大、溫度高、氧化嚴(yán)重,因此,為適應(yīng)風(fēng)口惡劣的工作環(huán)境,選擇了抗熱震、抗氧化、抗渣、抗堿的Sialon與SiC磚組合磚或賽隆剛玉磚,也可采用大型剛玉預(yù)制塊或硅線石大磚。
爐缸-爐底部分:內(nèi)壁采用導(dǎo)熱較低的陶瓷杯陶瓷墊組合而成的爐底陶瓷杯綜合工藝。瓷杯:選配剛玉磚組合陶瓷墊片:上層選用低鋁莫來石保護(hù)磚,第二層選用剛玉莫來石磚。
為降低散熱率,在爐體內(nèi)砌筑一層厚345~1150毫米的耐火磚,在爐體內(nèi)設(shè)置了冷卻裝置,防止?fàn)t殼變形。由于高爐各部磚襯損壞機(jī)理不同,為防止局部爐襯先損壞,應(yīng)根據(jù)爐體損壞、冷卻、高爐運(yùn)行等因素,選擇不同的爐襯,以防止?fàn)t襯損壞。傳統(tǒng)爐缸、爐底采用高級(jí)和超高級(jí)粘土磚。此磚已逐漸熔損,因收縮及砌磚質(zhì)量較差,過去常造成嚴(yán)重?zé)┦鹿,現(xiàn)爐缸、爐底多采用碳素耐火材料,基本解決了爐底燒穿問題。爐底使用的碳磚有三種類型:全部是碳磚;爐底四周和上部是碳磚,爐底的是粘土磚或高鋁磚;爐底的四周和下部是碳磚,上部為粘土磚或高鋁磚。后者又稱綜合爐底。而設(shè)計(jì)的爐底厚度有減薄趨勢(shì)(從0.5d右降到0.3d左右,或者1/4爐殼內(nèi)徑,d為爐缸直徑)。碳磚的缺點(diǎn)是容易被空氣、二氧化碳、蒸汽和堿金屬侵蝕。尤其是在爐下部的爐腰,因其磨損、熱應(yīng)力、化學(xué)腐蝕等原因,易損壞。高爐有冷卻壁,投產(chǎn)兩年左右,經(jīng)常出現(xiàn)爐身下部磚襯全腐蝕。在爐體上部及爐喉磚襯里要求耐磨性和耐熱穩(wěn)定性,粘土磚為宜。爐腹磚襯腐蝕后以“渣皮”維持生產(chǎn)。
近年來采用噴補(bǔ)工藝對(duì)磚襯進(jìn)行修補(bǔ)的方法已相當(dāng)普遍。噴補(bǔ)高鋁質(zhì)耐火材料(含Al2O340~60%),使用壽命為砌筑的3/4。
煉鉛爐用耐火材料
鉛熔煉爐一般采用鼓風(fēng)爐和電熔爐,目前使用較多的鉛熔爐為鼓風(fēng)熔煉爐。
鼓風(fēng)爐身上部、煙道及爐底非工作層一般采用粘土磚砌筑,爐身下部用鉻磚和鎂磚做爐襯,風(fēng)口區(qū)因溫度高(個(gè)別部位可達(dá)到1500℃左右),加上熔渣和粗鉛熔液的侵蝕,工作條件較苛刻,一般以高級(jí)粘土磚、高鋁磚或鎂鉻磚為襯,爐床粘土磚上應(yīng)砌筑致密鉻磚、鎂磚、鎂鉻磚、鎂鉻磚、鎂鉻磚為襯,爐床粘土磚上應(yīng)砌筑致密鉻磚、鎂磚、鎂鉻磚、鎂磚等材料也可以用鎂磚做工作襯,也可以用鎂磚來砌筑。
電熔爐系采用電極加熱,一般采用鎂鉻質(zhì)耐火搗打料,側(cè)墻及整個(gè)爐底都采用鎂質(zhì)耐火搗打料制作,側(cè)墻、出鉛口和虹吸管的工作層則用鎂磚砌筑。
煉焦耐火材料
煉焦?fàn)t層將煤干餾獲得焦炭廈化工產(chǎn)品的熱工設(shè)備,主要由炭化室、燃燒器、爐頂、斜道、蓄熱空間和小煙道等組成。如圖121所示。
(1)碳化房耐火材料。本實(shí)用新型具有周期性,裝煤時(shí),爐墻表面溫度降到600℃左右,結(jié)焦木期爐墻面又升到1000-1100℃。所以,炭化室壁采用硅磚砌筑。碳化室兩端的爐頭,在千爐門打開時(shí),溫度從1000℃降到500c℃以下,越過爐門體積穩(wěn)定的溫度界限(570C),因此,應(yīng)選用抗熱震性好的制品,“前大部分材料都選用粘土磚,現(xiàn)在傾向于選用高質(zhì)量鋁磚、硅線石磚和紅柱石砌筑。
(Z)l燃燒室燃耐火材料。燃燒室與炭化室共用爐墻,絨毛與炭化室相同。
(3)耐火材料用于爐頂。爐上煤孔周圍園溫波動(dòng)較大,采用粘土磚砌筑,其它部位采用硅磚。
(4)耐火材料用于斜道。通過斜道將燃燒室與熱室連接,要求磚體結(jié)掏穩(wěn)定,抗熱應(yīng)力作用。小焦?fàn)t用帖土磚,大中型焦?fàn)t采用硅磚砌筑。
(5)再生室用耐火材料。小焦?fàn)t蓄熱室的單立墻、隔墻和底柏格磚砌筑速率用粘土磚砌筑,大中型焦?fàn)t蓄熱室中、上部砌體全部采用磚砌筑,以使焦?fàn)t整體內(nèi)隔墻砌筑,
(6)用于小型管道的耐火材料。煙道位于蓄熱室底部與煙道相通。
這些小煙道都是用牛糞砌成的。
總體而言,焦?fàn)t耐火材料目前以硅磚為主。煉焦硅磚
對(duì)外觀尺寸要求精確,且體積密度、熱導(dǎo)率、高溫蠕變性和高溫強(qiáng)度足夠高;磚中物相成分主要是石英鱗片,殘存石英較少。
推薦新聞