產(chǎn)品展示
| PRODUCT您的當前位置:首頁 > 新聞動態(tài) > 產(chǎn)品知識 > 正文
正文
硅磚生產(chǎn)工藝介紹
發(fā)布時間:2022/6/9 11:14:02 點擊率: 來源:高鋁磚廠家 作者:榮盛耐材 硅磚的價格居高不下,因為是成品率低,某一環(huán)節(jié)出現(xiàn)問題就會受到影響,下面介紹一下硅磚的生產(chǎn)工藝,請看詳細內(nèi)容。
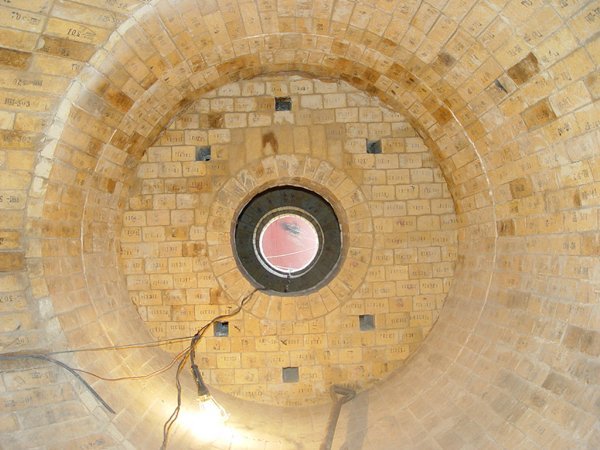
硅磚生產(chǎn)的工藝流程大體上與粘土磚的工藝流程相似。不同點在于前者增加了石灰和礦化劑的制備系統(tǒng)。
一、顆粒組成的選擇
硅質(zhì)坯體加熱時的松散和燒結(jié)能力取決于顆粒組成中粗細兩種粒度的性質(zhì)和數(shù)量。
采用細顆粒組成的磚坯時,在燒成時有利于減少膨脹,減少磚體的裂紋和體積變化,提高成品率,還可提高制品中鱗石英的含量,但泥料顆粒過細,也將導致硅磚氣孔率的提高。
一般硅磚的臨界粒度以2~3mm為宜。
制造硅磚選用的結(jié)合劑
制造硅磚用的結(jié)合劑有亞硫酸紙漿廢液和石灰乳。用石灰乳作結(jié)合劑時,它起著塑化劑的作用。石灰乳使磚坯在干燥過程中增加強度,在燒成時則成為礦化劑,促進石英的轉(zhuǎn)化。
石灰應含有大量活性CaO,未分解的CaCO3和MgCO3不超過5%,Al2O3+Fe2O3+SO2F超過5%。當含有大顆粒欠燒Ca-CO3和過燒石灰時,制品產(chǎn)生熔洞,影響制品質(zhì)量。
配料時應將石灰的加入量換算成CaO,其加入量視制品的不同而異,通常波動在1.5?2.5%。例如,生產(chǎn)焦爐硅磚,CaO加入量為2.0?3.0%;生產(chǎn)電爐頂硅磚,CaO加入量為1.4?1.75%。
硅磚的配料特點
采用雜質(zhì)含量小于0.5%的優(yōu)質(zhì)硅石,配料前用自來水沖洗,以保證前期質(zhì)量。配料時將快轉(zhuǎn)化石英與慢轉(zhuǎn)化石英混合配料,可使燒成溫度降低20℃。配料過程中將臨界粒度由3mm降至2mm,可增加物料的界面能,促進石英的轉(zhuǎn)化。
此外,選用新型礦化劑,對提高產(chǎn)品質(zhì)量也很重要。目前,大多數(shù)生產(chǎn)者在配料中加入的礦化劑仍是石灰乳和鐵鱗。為提高制品的荷重軟化溫度,F(xiàn)eO的加入量已從2.5%降至1%以下。如果采用長石類含有堿金屬的礦物或復合礦化劑都可以收到較好的效果。
制備硅磚泥料的加料順序
將各種硅石粉和廢硅磚粉按一定配比加入濕碾機中,先干混2?3min,再加入亞硫酸紙漿廢液、石灰乳及氧化鐵粉的混合液,根據(jù)成型方法的要求,再混合8?17min。
泥料混合時間的長短取決于碾輪重量、碾盤轉(zhuǎn)數(shù),原料加入量、原料硬度、泥料的顆粒組成及成型方法。特異型磚和手工成型用的泥料比機械成型用的泥料要求有較長的混合時間。對于不同泥料的混合時間,應由實驗來確定。
制造硅磚用泥料的水分一般為5?9%,手工成型泥料水分為7?9%,機械成型用泥料水分為5?6%。
二、成型:
硅磚成型的特點表現(xiàn)在硅磚坯料成型特性和硅磚磚型形狀復雜與質(zhì)量差別大等方面。硅質(zhì)坯料是質(zhì)硬、結(jié)合性和可塑性低的瘠性料,因此它受壓而致密的能力低。硅質(zhì)坯料的成型性能受其顆粒組成、水分和加入物的影響。調(diào)整這些因素可以改善坯料的成型性能。對任何組成的坯料,增加成型壓力都會提高硅磚密度。為了保證制得致密磚坯,成型壓力應不低于100~150MPa。
三、燒成
硅磚在燒成過程中發(fā)生相變,并有較大的體積變化,加上磚坯在燒成溫度下形成的熔液量較少(約10%左右),使其燒成較其它耐火材料困難得多。硅磚的燒成制度與磚坯在燒成過程中所發(fā)生的一系列物理化學變化,加入物的數(shù)量和性質(zhì),坯體的形狀大小以及燒成窯的特性等因素有關(guān)。
1、硅磚在燒成過程中的物理化學變化在150℃以下從磚坯中排出殘余水分在450℃時,Ca(OH)2開始分解;450~500℃時Ca(OH)2脫水完畢,硅石顆粒與石灰的結(jié)合破壞,坯體強度大為降低。在550~650℃范圍內(nèi),b—石英轉(zhuǎn)變?yōu)棣痢,由于轉(zhuǎn)變過程中伴有0.82%的體積膨脹,故石英晶體將出現(xiàn)密度不等的顯微裂紋。
在600~700℃間,CaO與SiO2的固相反應開始,磚坯強度有所增加,反應式為:
2CaO+Si02→b一2CaO·SiO2
2CaO·Si02+Si02→2(CaO·Si02)
至1000~1100℃有固熔體狀α-CaO·Si02與FeO·SiO2生成。
α-CaO·SiO2+FeO·SiO2→[GaO·SiO2—FeO·SiO2]
從l100℃開始,石英的轉(zhuǎn)變速度大大增加,磚坯的密度也顯著下降,此時磚坯體積由于石英轉(zhuǎn)變?yōu)榈兔芏茸凅w而大為增加。雖然此時液相量也在不斷增加,但在1100~1200℃范圍內(nèi)仍易產(chǎn)生裂紋。
在1300~1350℃時,由于鱗石英和方石英數(shù)量增加,磚坯的密度降低得很多。此時液相粘度仍較大,對內(nèi)應力的抵抗性還弱,生成裂紋的可能性存在。當加熱到1350~1430℃時,石英的轉(zhuǎn)變程度和由此產(chǎn)生的磚體膨脹大大增強,在這一溫度范圍內(nèi),加熱得愈緩慢,石英溶于液相再結(jié)晶生成的鱗石英量愈多,方石英生成量愈少,磚體生成裂紋的可能性也愈小。如果加熱過快,特別是在氧化氣氛下迅速加熱,石英轉(zhuǎn)變?yōu)榉绞,使磚坯松散并出現(xiàn)裂紋。
2、燒成制度
在600℃以下,可用較快而均勻地升溫速度燒成。 在700℃以上至1100~1200℃溫度范圍內(nèi),因磚坯體積變化不大,強度逐漸提高,不會產(chǎn)生過大應力,只要保證磚坯加熱均勻,可盡快升溫。
1100~1200℃至燒成終了溫度的高溫階段,硅磚的密度顯著降低,晶體轉(zhuǎn)變及體積變化集中地發(fā)生在這一階段。它是決定磚坯出現(xiàn)裂紋與否的關(guān)鍵階段。這個階段升溫速度應逐漸降低,并能緩慢均勻升溫。
為了在高溫階段使溫度緩慢均勻上升,在生產(chǎn)中通常采用弱還原火焰燒成。同時還可以使窯內(nèi)溫度分布均勻,減少窯內(nèi)上下溫差,避免高溫火焰沖擊磚坯,達到“軟火” (均勻緩和火燒成)燒成要求。
硅磚高燒成溫度不應超過1430℃。
硅磚燒成至高燒成溫度后,通常根據(jù)制品的形狀大小,窯的特性,硅石轉(zhuǎn)變難易,制品要求的密度等因素,給以足夠的保溫時間。硅磚燒成后的冷卻,高溫下(600~800℃以上)可以快冷,低溫時因有方石英和鱗石英的快速晶型轉(zhuǎn)變,產(chǎn)生體積收縮,故應緩慢冷卻。
在制定燒成曲線時,除應符合上述要求外,還應考慮:
1)原料的加熱性質(zhì);
2)加入物的數(shù)量和性質(zhì);
3)磚塊的形狀大小。其他如燒成窯的結(jié)構(gòu)、大小、裝窯方法、窯內(nèi)溫度分布等均有影響。
燒成升溫速度一般可劃分為如下幾個階段;
溫度范圍,℃ 升溫速度℃/h
20~600 20
600~1100 25
1130~1300 10
1300~1350 5
1350~1430 2
- 上一篇:低蠕變高鋁磚的低蠕變是什么?
- 下一篇:高鋁磚用耐火泥配置方法